How to Fix the Greatest Threat to Reliability and Resilience
A Primer on Digital Risk Mitigation
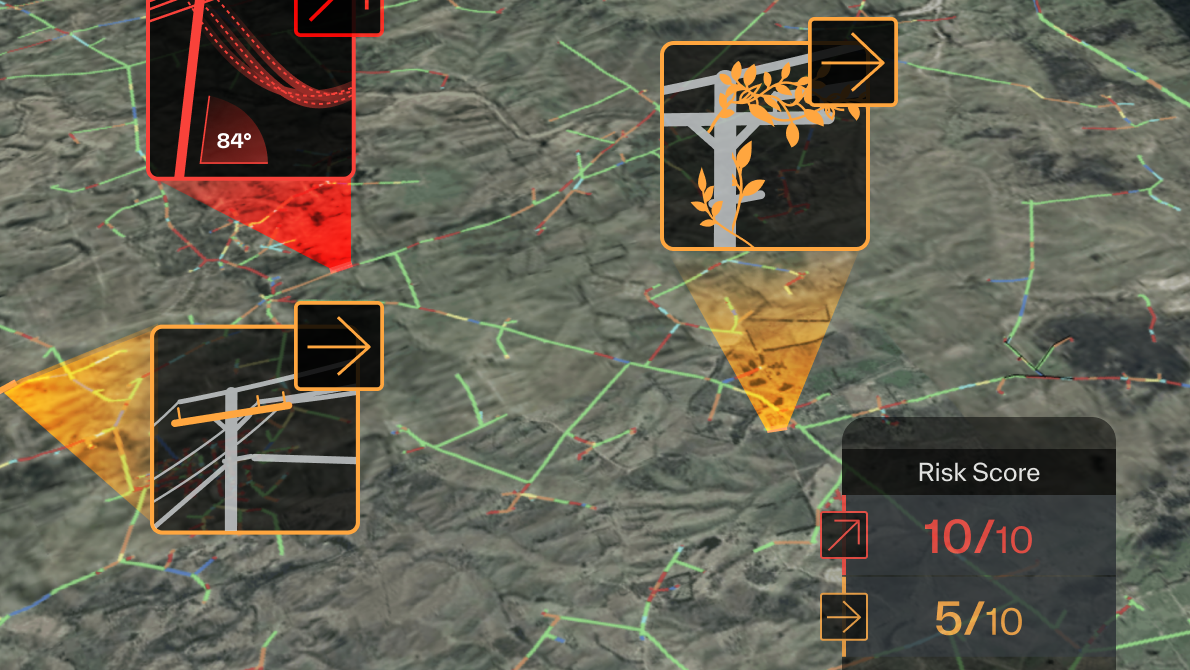
You wouldn’t ignore a large swath of spans at high-conductor clash risk alongside a major highway because there are another five months until the next scheduled inspection. You wouldn’t replace a failing pole that would cause far fewer downstream outages than another with a lower failure impact. Or resolve a vegetation clearance risk that’s 14.3 feet from a line before resolving another 3 inches from a line. But things like this happen daily.
Why? Because risk discovery and remediation processes and policies have failed to keep pace with the challenges utilities face today — and the technology available to them.
In an industry rightly obsessed with mitigating risk, risks, and mitigants are deeply embedded in the collective consciousness. Every decision-maker, field crew, engineer, and policymaker knows that risks aren’t created equal in urgency or impact. Neither are the range of solutions to address them. Yet current risk discovery and remediation processes and the regulations that inform them often fail to acknowledge this.
Too often this failure undermines utilities’ best efforts to improve reliability and resilience and results in bad outcomes for them and the communities they serve. In fact, US utility fines and violations have increased 800% in the last five years compared to the prior five-year period.
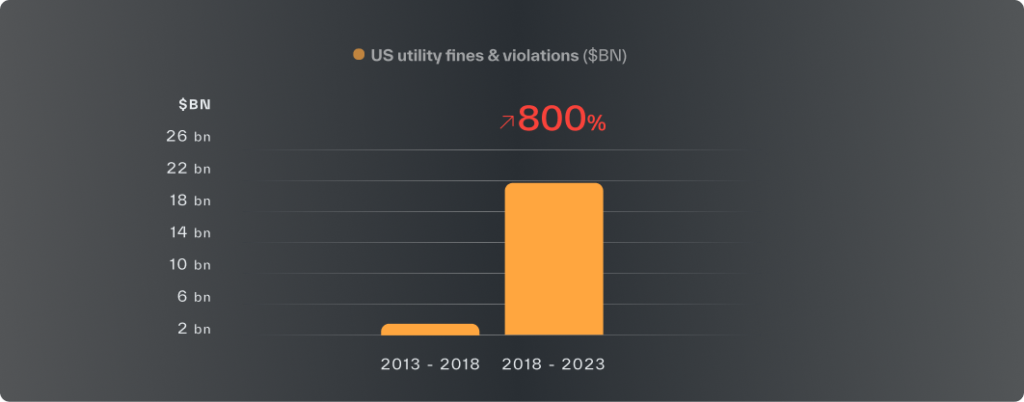
Three Major Shortcomings of Legacy Processes and Policies
How did we get here? Here are three critical shortcomings that explain the disconnect.
1. Utilities are discouraged from proactively identifying risks.
Picture this — an inspector spots new construction converging on safe clearance to an existing pole. Some agencies would require that inspector not leave the field until they have satisfactorily mitigated the risk — in this case, relocating the pole.
Many regulatory jurisdictions mandate utility personnel to remediate risks immediately, or within a tight timeframe, upon discovery. No one wants risks festering unattended, but this expectation actively discourages proactive behavior, as you can only prevent risks from unleashing danger and damage if you know about them in advance. But in today’s regulatory landscape, utilities are fearful of retribution for knowing about anything in advance — especially when they don’t have the resources to address every risk right away.
Is it better to force utilities to keep reacting to a mixed bag of tasks with unknown impact and look the other way from ticking time bombs for fear of criminal liability? Or to make sure utilities have the support and resources they need to proactively deliver on their resilience and reliability promises?
Processes and regulations must acknowledge that risks are not created equal and must be proactively prioritized and addressed in order of impact, not discovery. Today’s black-and-white ‘it’s a risk or it’s not’ framework must evolve to reflect well-defined, context-rich shades of gray. This way, both utilities and regulators can standardize exactly what constitutes “urgent” and “high-impact” and encourage utilities to adopt a more proactive approach to reliability and resilience.
2. Risks are defined in a vacuum.
Inspectors often flag risks, such as leaning poles, during field visits on a fair weather day. On a > 100-degree day, sagging conductors can create vegetation risks you wouldn’t see on a fair weather day. 75 mph winds may cause conductors to gallop, causing outages, on spans that seemed to bear even tension on inspection day. Flash floods could destabilize vegetation and cause fall-in risks you might not otherwise worry about.
It’s never been more critical to understand how your assets will behave in every scenario, not just the conditions where it’s safe to conduct manual surveys.
Too often, risks are defined in a vacuum according to decades-old standards, not in the context of real-life operational conditions. Someone somewhere might have decided that >40 mph constitutes “high winds”, creating standards dictating that poles must withstand 40 mph winds. But what if pockets of your network actually routinely experience >60 mph winds? Today’s high stakes demand that utilities and policymakers define risks in the context in which they become dangerous, with the flexibility to stress-test and recalibrate existing assumptions.
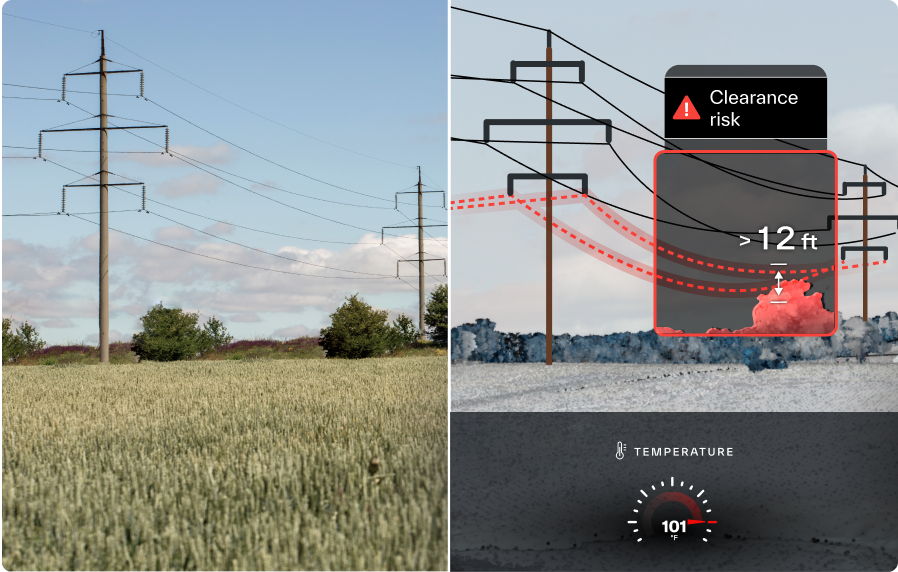
3. Remediation is a one-size-fits-all exercise instead of targeted cost-benefit trade-offs.
When you are required to respond to risks immediately upon discovery, there isn’t much room to thoughtfully evaluate the best solutions. For example, rather than defaulting to pole replacement, simply adding a stay or replacing just the cross-arm can often achieve the desired effect. If only you knew where and could execute as such, this approach could save millions of dollars annually.
How much stronger would your request for pole hardening dollars be if, instead of suggesting you replace all wooden poles with composite or steel, you could prove exactly which wooden poles present failure risk and the expected network performance improvements?
If utility executives, network operators, inspectors and regulators all agree that risks and mitigants aren’t created equal in urgency or impact, why is the default approach so at odds with what they know to be true?
While manual inspections will continue to play a critical role in network governance, they are dangerously insufficient as a standalone strategy for improving reliability and resilience. Relying on manual inspections for risk discovery instead of focusing them on validation and triage hinders utilities’ ability to align actions and philosophy.
Here’s Why Manual Field Surveys Aren’t Enough
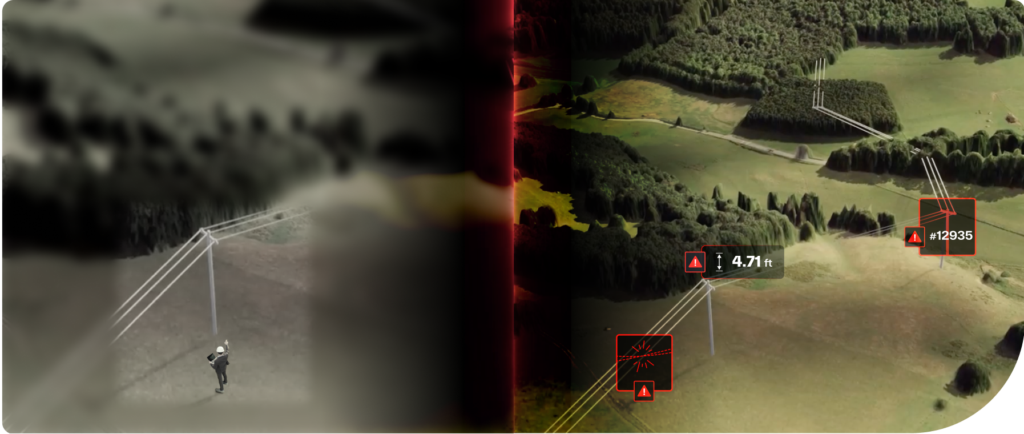
1. You can’t prioritize risks you can’t see.
A field survey team can only cover an area of a few hundred poles in a single field visit, or a small percentage of a >20k mile network area. Counting on manual field surveys on a cyclical inspection cycle as a first line of defense is like limiting an annual physical to your left arm when your right leg is broken.
2. You only see your assets on their best behavior.
When did you last send a field team out to inspect equipment in >100 mph winds and flash flood conditions? Hopefully, never. However, with a 74% increase in severe weather-related outages in the last decade, severe weather conditions are the most important conditions to ensure your assets are prepared for — not the 65-degree and sunny day when your next inspection is scheduled.
3. You can’t improve what you can’t measure.
It’s unlikely that inspectors can realistically examine every single asset and all vegetation in great detail — but that doesn’t mean guesstimating critical metrics like pole lean angle and ground clearance is “good enough.”
If two poles are both marked “approx. 80 degrees”, how can you expect your team to prioritize remediating the one that is factually leaning at 85 degrees instead of the one leaning at 72 degrees?
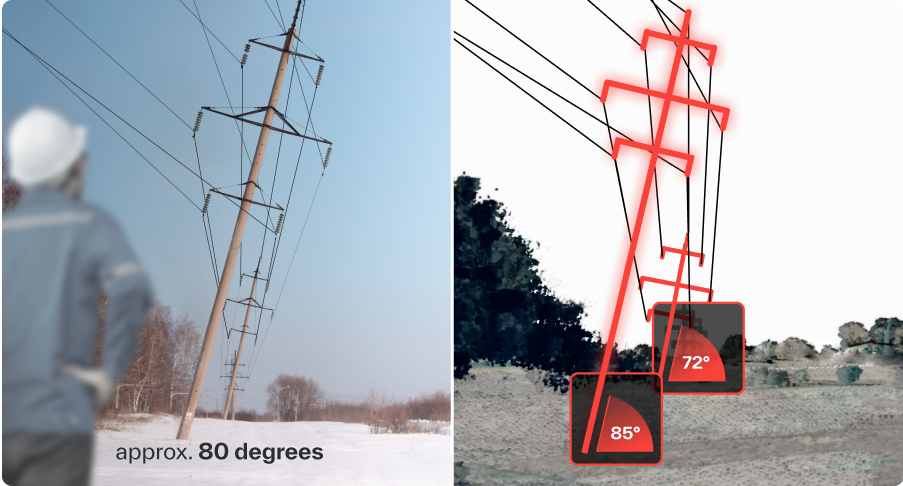
Even tools like laser range finders are often insufficiently accurate in measuring line tension imbalances, for example, to justify maintenance work.
Here’s what’s more insidious — you can’t connect your team’s hard work directly to outcomes. Did replacing those 5k poles result in fewer pole failures? Did reconductoring result in lower maintenance costs? Did additional vegetation maintenance lead to fewer wire-down safety incidents?
Did each of these initiatives simply seem like a directionally positive investment, or can you demonstrate each initiative’s direct contribution to reduced outages, cost-effective resilience, and improved customer satisfaction? How can you be sure the investments you make are actually going to solve your problems?
If you can’t measure outcomes, you can’t demonstrate that you’re improving them. And if you can’t demonstrate that you’re improving outcomes, you will struggle to secure the budget you need from regulators to meet your biggest challenges.
Manual risk discovery creates a gulf between utilities’ and regulators’ understanding of how to solve these challenges. This disconnect is more apparent than ever, with the average rate increase request approved by regulators slashed nearly in half over the last few years.
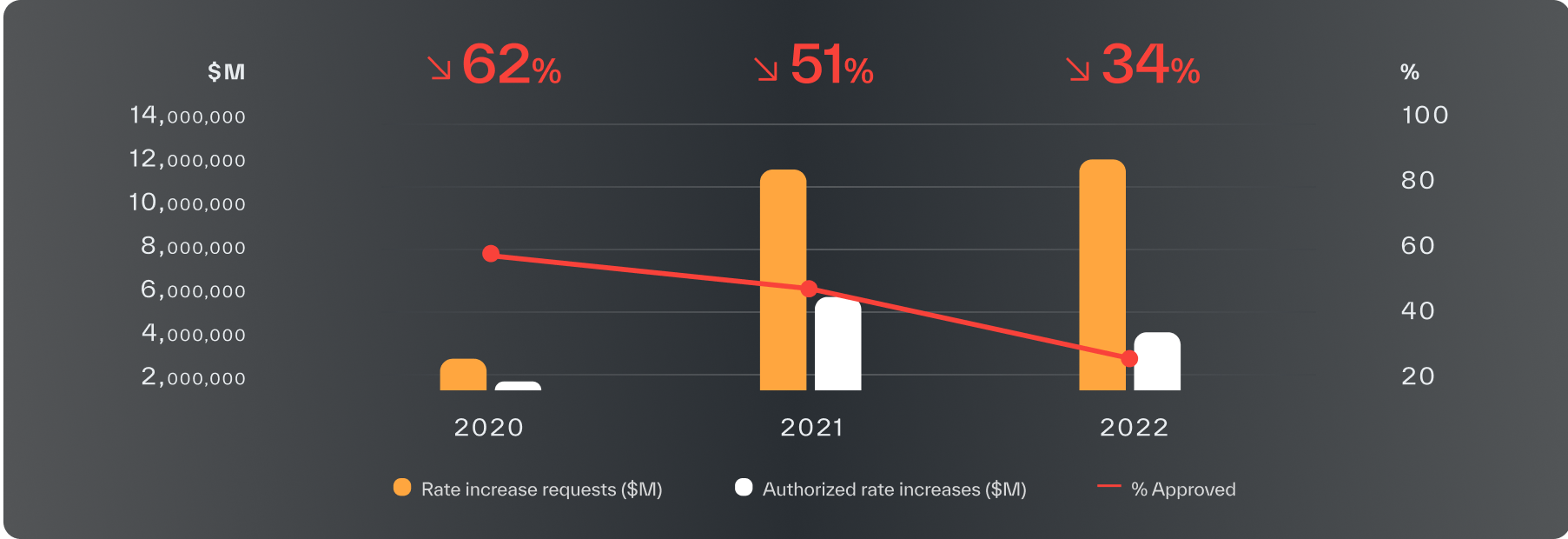
As long as your most important projects are documented as papered work orders with the lifespan of any given field operation, measuring outcomes is a subjective process that can take weeks of manual data entry and analysis. If regulators can’t audit your field operations and clearly see how outcomes are improving, they will continue to question your priorities, and you will be left with the burden of proof — and the burden of resolving any documented risks.
Policies and processes must evolve to support more proactive risk-reduction efforts and encourage utilities to deploy predictive technology to stay ahead of risks while reserving manual inspections for a more targeted and impactful role in triage and remediation.
If field teams were less pressured to carefully examine every asset and instead could direct their attention to pre-flagged risks, they could use their expertise to introduce a much-needed triage layer between risk discovery and remediation. Utilities could graduate from reacting to risks to a proactive approach that ultimately improves outcomes, reduces fines, and removes friction from the ratemaking process.
Utilities have been able to restore power 3x faster with Neara
How to use predictive modeling technology to proactively discover and mitigate risks
AI-driven predictive modeling software can lay a powerful foundation for a proactive approach to de-risking everything from new network design, equipment inspections, vegetation management, and beyond. AI-driven software can handle the bulk of the legwork in taking a first pass at flagging risks that meet custom thresholds your team sets. AI can process enormous volumes of data, as well as efficiently and consistently navigate relationships between different data sets. As a result, it can be a formidable force-multiplier to manual inspections by directing precious expertise where it’s needed most.
However, a key advantage is that software can cover your entire network at once, not just a few hundred poles at a time, giving you the confidence that your team’s attention is exactly where it needs to be. Discovering risks digitally also offers flexibility to define and reset risk thresholds, simulate different weather conditions and mechanical variables, and easy-to-audit outputs you can share to measure outcomes and validate your approach.
1. Using data sources you’re likely to have already, populate a digital model of your network.
Data sources include GIS, LiDAR, imagery, pole libraries, construction standards, and more. Many utilities are looking to purpose-built software to build hyper-accurate, custom-engineered network models that are geometrically and behaviorally identical to your real-life assets, so every asset bends, sags, deforms, and sways exactly the same way your real-life assets would in response to stimuli like heat and wind.
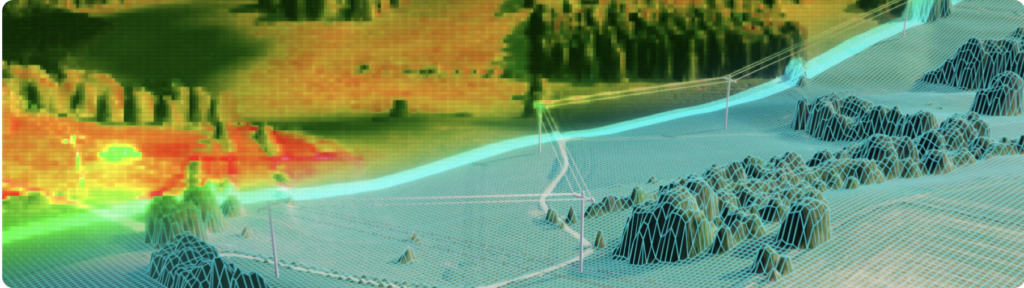
2. Correct data errors and confirm the exact location of every asset, vegetation type, and clearance object.
The combination of data sources in a digital model can automatically, and quickly, reveal and fix errors in your data. This means that you will never again send a team into the field for maintenance to the wrong location.
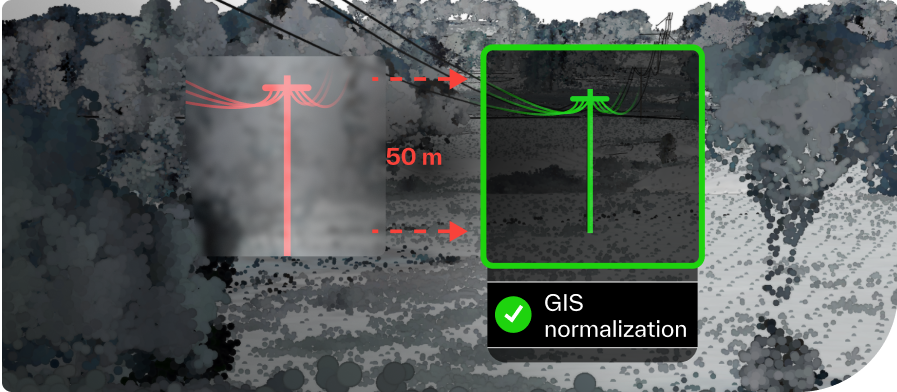
3. Conduct in-platform surveys, including severe-weather stress tests.
In Neara’s software, you can simulate hundreds of environmental and mechanical variables and get a detailed report on how every single asset will respond. Outputs include pole loading risks, areas where conductor clashing is likely, roadway clearance breach risks, vegetation fall-in, and encroachment risks. Then, findings at the individual asset level roll up to system-wide assessments you can use to demonstrate improved reliability and resilience clearly.
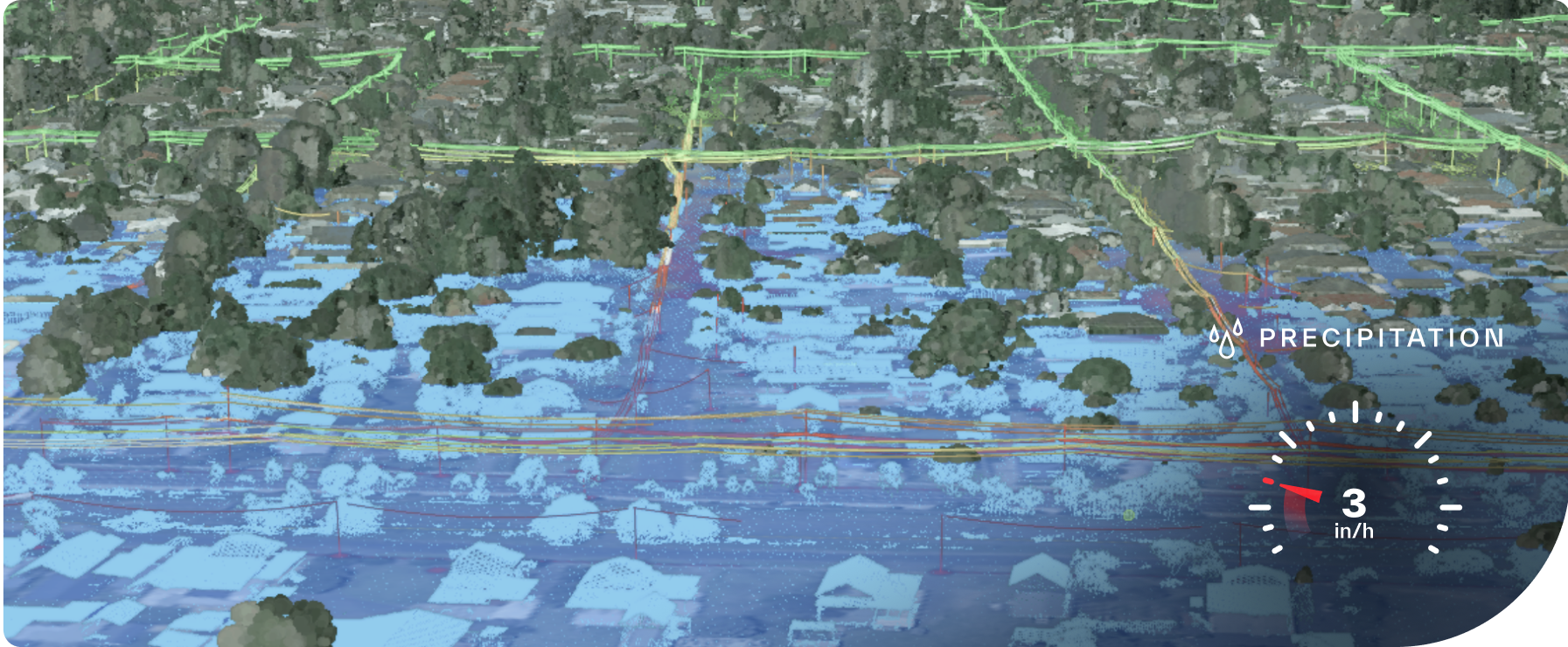
4. Execute triage according to rigorously and uniformly defined risk thresholds.
Identifying risks digitally means you will find orders of magnitude more of them in one “survey.” If that sounds overwhelming, rest assured that for the first time, you can tier risks according to criteria you define by urgency and impact. This step is critical in clarifying priorities and building transparency around a proactive approach.
At this stage, many realize that several manually flagged tier-one risks no longer make the cut. And among those that do, there’s often a great deal of variability in actual urgency — if your tier-one threshold is an eight-foot clearance, you probably want to prioritize the one just two inches from a line instead of 7.9 feet away.
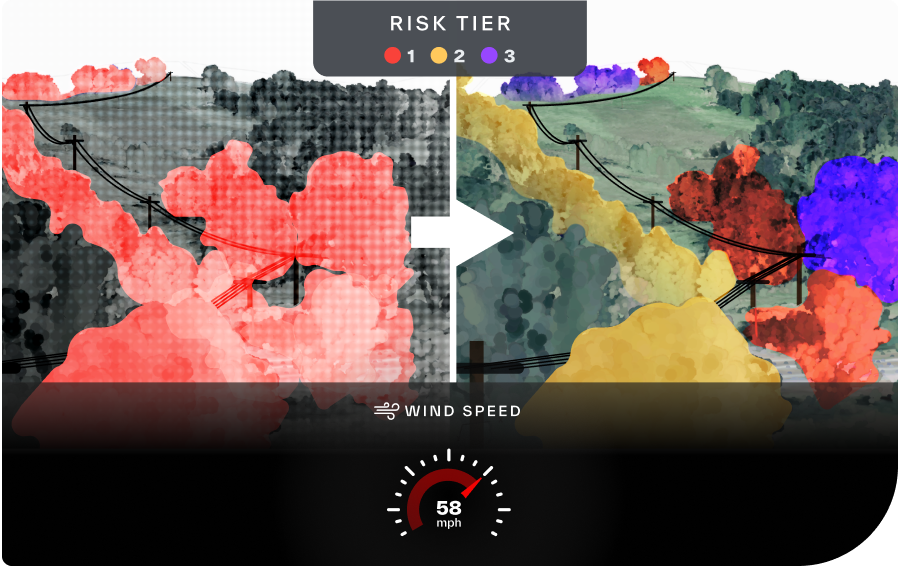
5. Run risk-reduction analyses, execute remediation and measure outcomes.
Based on risks you’ve identified, execute analyses in minutes and hours that would otherwise take months or more in the field. For example, show exactly where you need to replace wooden poles with composite ones and where it’s likely sufficient to simply add stays. Find the perfect route for net new network design. Explain every dollar of your vegetation budget, highlight specific spans where reconductoring will help you better prepare for a heat wave, and, most importantly, demonstrate that your approach is effective.