Resources
A Primer on Digital Equipment Inspections
Resources
Why digital equipment inspections are key to reducing outages, faults, and getting your network what it needs
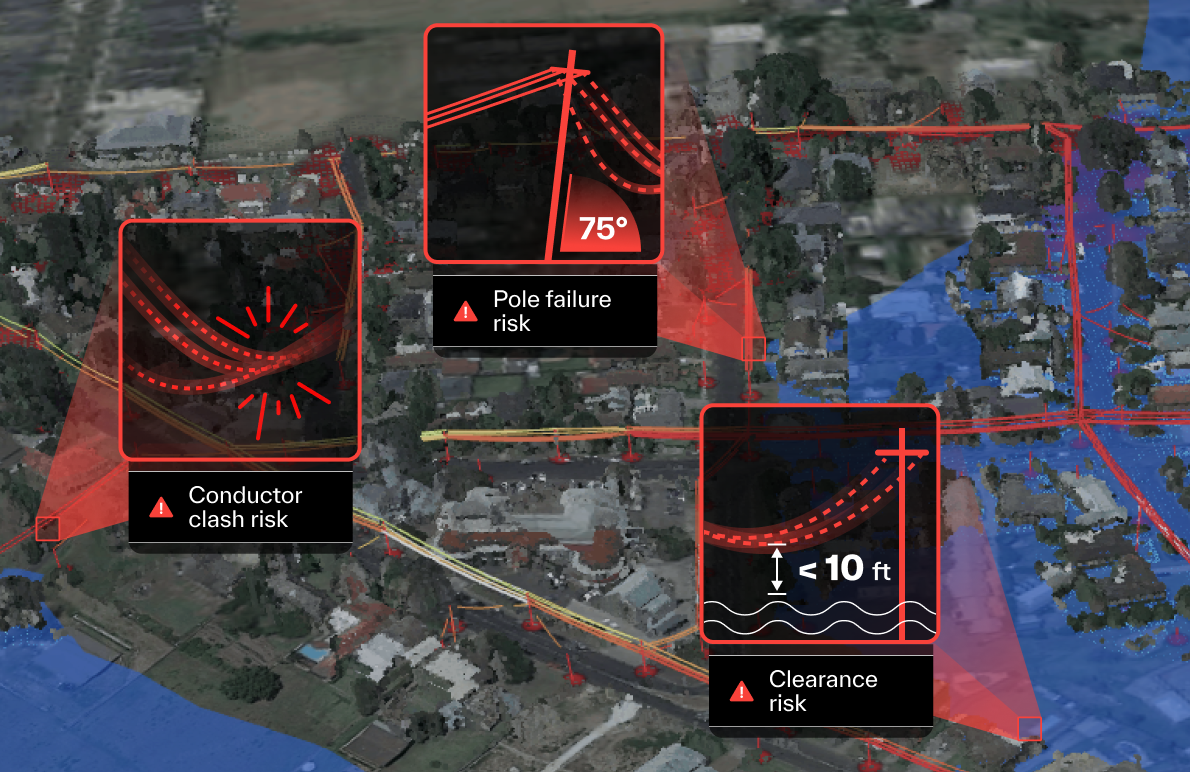
Your team knows every type of pole and conductor in every circuit, and you can probably hand-draw a color-coded map of your poles by age across most of your network based on recent replacement cycles.
But no matter how rigorous and thorough your inspection protocols are, you can only cover a couple hundred poles worth of network in one field visit. Even if you could clone your best inspector and have them examine every pole in your network at superhuman speed, it could still be weeks until their assessment translates into work orders.
Despite utilities’ best efforts, equipment is still at fault in too many safety incidents, from OSHA violations to large-scale wildfires. With severe weather causing 74% more outages in the last decade than in the prior decade, resilience is more important than ever.
As a result, equipment inspections today must be faster, more accurate, and more consistent than ever before. Utilities are turning to digital, AI-assisted equipment inspections using network modeling technology to cover more ground faster and set a new standard for precision.
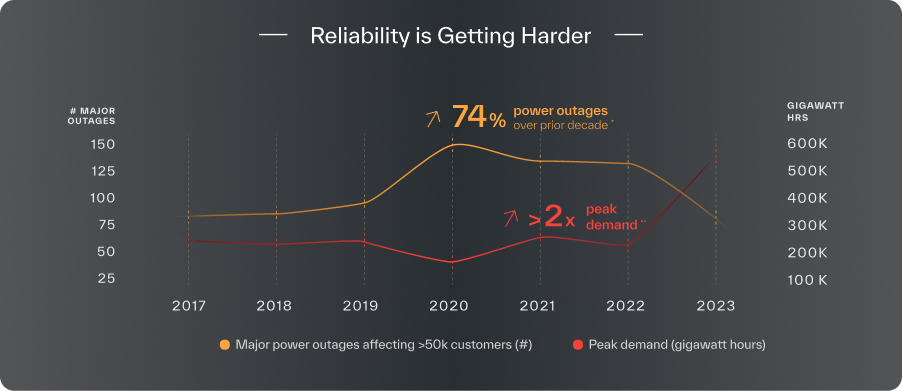
Raise the bar on speed and precision
The naked eye can see poles leaning at an exaggerated angle and crooked cross-arms. Your GIS can tell you how old your poles are. However, there’s much more to equipment health than age or than meets the eye.
Manual equipment inspections traditionally rely on strong visual cues and GIS data to highlight problem assets. However, some of the most insidious asset health issues can easily go unnoticed even with strict survey protocols — for example, a leaning pole at risk of failure that appears upright because of the angle of the ground underneath or a sagging conductor attributed to a warm day instead of creep. Clearance estimations, too, can be highly problematic even if they miss the mark by less than an inch.
Conducting in-depth manual inspections across every single asset in the entire network would be impractical, so it figures that inspectors focus their attention according to the information at hand. But the trouble is that the information at hand is incomplete at best.
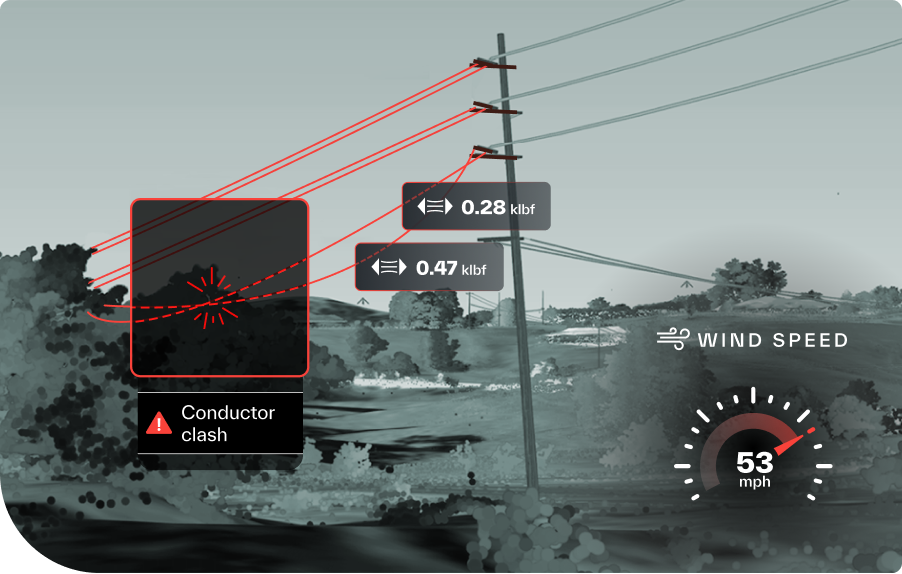
Geospatial data sources such as LiDAR and imagery fill in the blanks and help paint a complete, context-rich view of your network. Digital modeling technology can automatically combine multiple data sources into a single version of your network, replicating the real-life inspection environment. Each modeled asset behaves and responds to stimuli, from northeast winds to line tension, exactly as it does in the field. The only difference is that you can inspect your whole network instead of a few hundred poles at a time — without the truck rolls and the safety incidents.
Digital equipment inspections set a new standard for accuracy and speed in detecting structural defects with MRI-like precision, even if they appear in good condition, much faster than ever possible in the field. When your team spends less time walking the field and manually answering hundreds of questions per pole, they can focus more on creative ways to correct and prevent asset deformities and structural integrity issues. This way, you can also improve the quality of the corrective solutions your team can execute.
A wildfire-prone utility facing high conductor clash frequency initially estimated its risk mitigation project would take three years. With AI-assisted digital equipment inspections, the project took less than four months. The utility used its digital model to automatically surface minor but consequential differences in span-to-span line tensioning that increase conductor clash risk with far more precision and consistency than the human eye could reliably identify.
See how one utility identifies conductor clash risks 10x faster with Neara
Ensure high-priority risks are, in fact, high-priority risks.
Your network’s sheer size and complexity guarantee that something will always need your team’s attention — and the stakes are too high to risk directing your attention anywhere but where it’s needed most. A fundamental weakness of manual equipment inspections is that the human brain is highly adaptable and excels at relativity when the context calls for absolutism and consistency, which will ensure you carefully prioritize which risks to address and in what order.
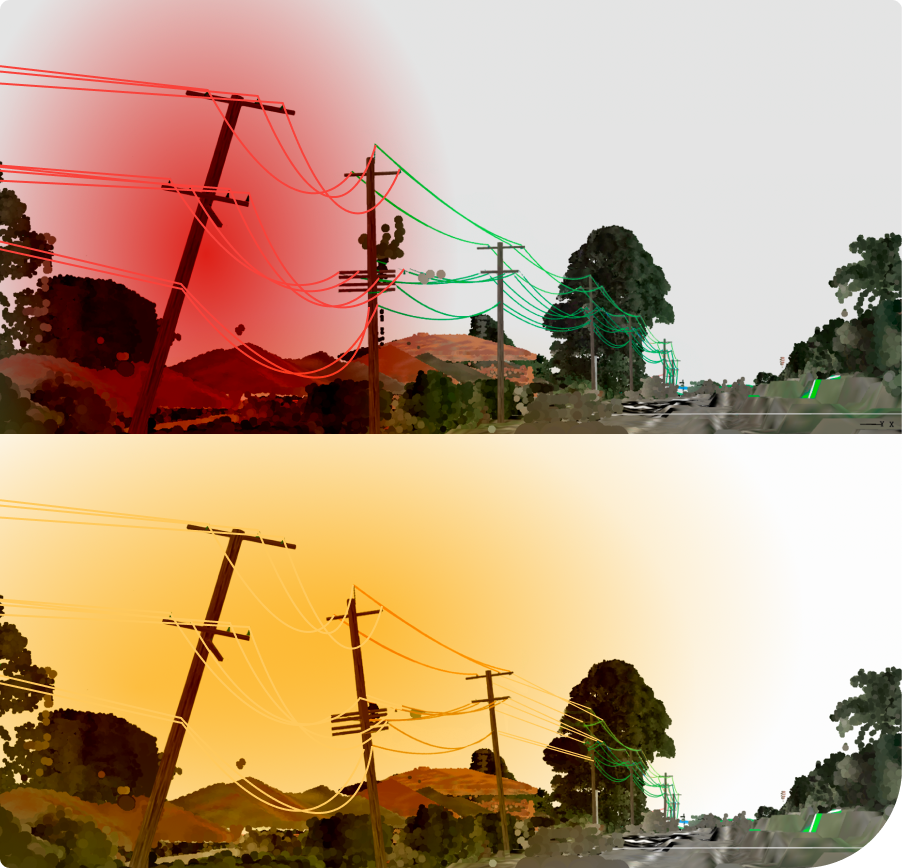
A slightly leaning pole amongst 100 perfectly upright poles may seem glaring, but when you see that same pole amid 100 other poles in various stages of disrepair, it will likely jump to the back of your priority queue. Digital inspections solve for sample size bias by enabling inspectors to evaluate every asset simultaneously against the same criteria, instead of only the asset sample inspectors can observe in a single field survey. The result? Objective, data-driven asset health diagnostics.
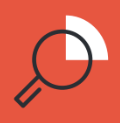
A hurricane prone utility identifies every high-risk pole within 24 hours
For example, one hurricane-prone utility set a threshold for high-failure risk poles at a 17% lean angle — they needed to urgently identify poles at 17% lean or greater and couldn’t afford to divert any resources to lesser risks. Within 24 hours, they used their digital network model to identify the lean angle of every pole in their network and then filtered the report to those at 17% or greater.
Not only would it otherwise have taken weeks at minimum to canvas every pole in the network, but even if field teams could examine every pole in one day, they would find it very difficult to enforce the precise 17% threshold — especially with the stress of an imminent emergency situation.
Translate “as-surveyed” to any scenario with AI-assisted simulations.
Most equipment inspections occur on fair weather days, even though many of the worst safety incidents occur in extreme weather conditions. While you would never send your team out in a hail storm, a hurricane, or dangerously high temperatures, these are the critical scenarios you need to ensure your assets can withstand.
Digital modeling software with simulation functionality allows you to inspect your equipment under any condition by bringing hundreds of mechanical and environmental variables to life in your model. This allows you to avoid being caught off guard by the real thing in the field.
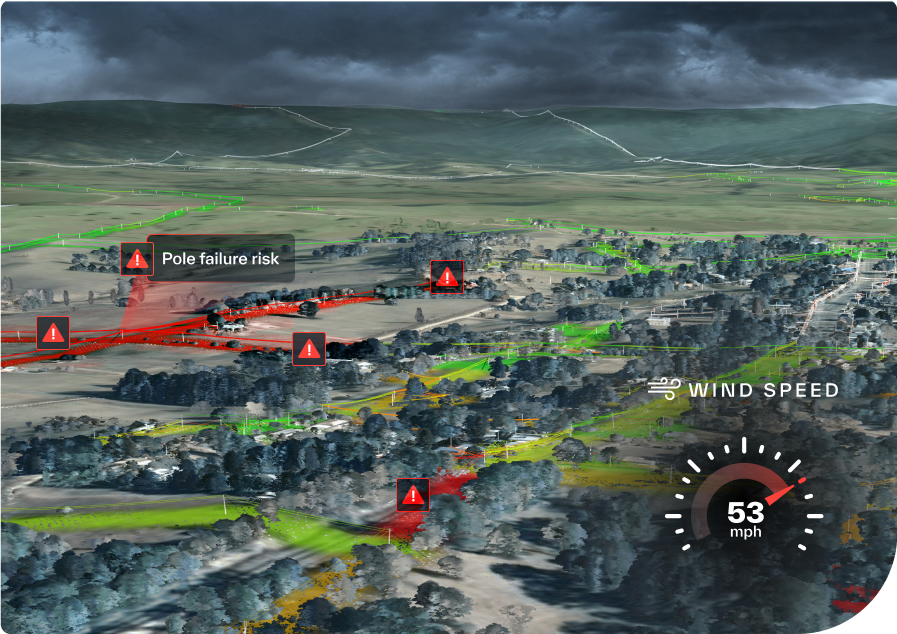
By simulating storm conditions such as high winds, your digital model gives you a heatmap for where you need to replace failure-risk poles, install stays, or take alternative measures to improve structural integrity. By seeing how every span will behave in high winds, your model pinpoints spans where installing spacers or adjusting line tension will significantly reduce conductor clash risk. In a flash flood scenario, you can examine water levels to see where to replace poles with flood-resilient materials.
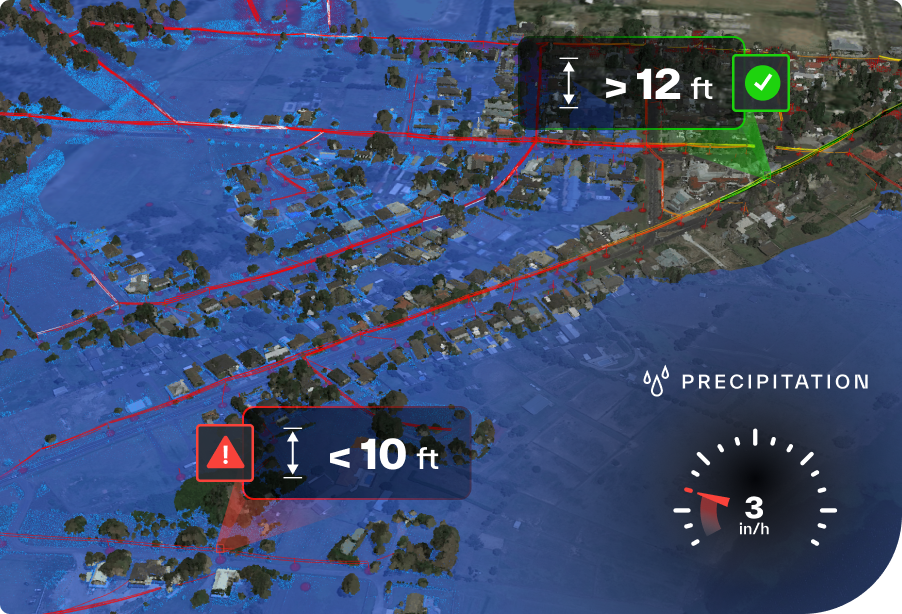
Improve data quality to get your network what it needs.
Network-wide digital equipment inspections go beyond strengthening your physical asset resilience — they also vastly improve your team’s data quality. Every time you run an analysis, discover a risk, create or close a work order, digital modeling software automatically creates
data outputs that contribute to an ever-growing database of the steps you’ve taken to fortify your network and their impact.
Without extra effort or administrative tasks, you’re passively creating a digital data trail that objectively defines network needs instead of relying on anecdotes and assumptions. The outputs are legible to other stakeholders, from other field teams to regulators — meaning they can deliver actionable insight in a language and format they understand without extensive training on your team.
When every equipment repair becomes a durable, digital artifact instead of a papered work order with the lifespan of any given field operation, you infuse all operations with consistency. Every time you replace or relocate a pole, your vegetation team’s clearance calculations automatically update. Your underbuild clearance reports and your GIS stay up to date.
When you’re building your rate case, instead of inviting skepticism and months of back-and-forth, your model helps you clearly define network needs with high-quality data straight from your digital inspections. Showing the process for identifying and prioritizing network needs can make the difference between approval and getting stuck in a reactive cycle where you take the heat for equipment faults with too many variables beyond your control.
Digital equipment inspections put you back in control of a constantly shifting environment with the flexibility to define thresholds and simulate crucial variables in a digital environment so you can prepare for anything. They empower you with predictive visibility into how your assets will respond to stresses you can’t see in traditional manual inspections. This way, you’re ready to prioritize, budget for, and execute risk mitigation operations ahead of floods, fires, and more. And ahead of the rate case season, you know exactly what to ask for and how to justify the ask.
Reach out. We’re very friendly.
Contact us to learn more, schedule a demo, inquire about a pilot project, or discuss other needs.